Mastering Flow - A Focus on Pressure Regulators
Published date: 08 Aug 2023
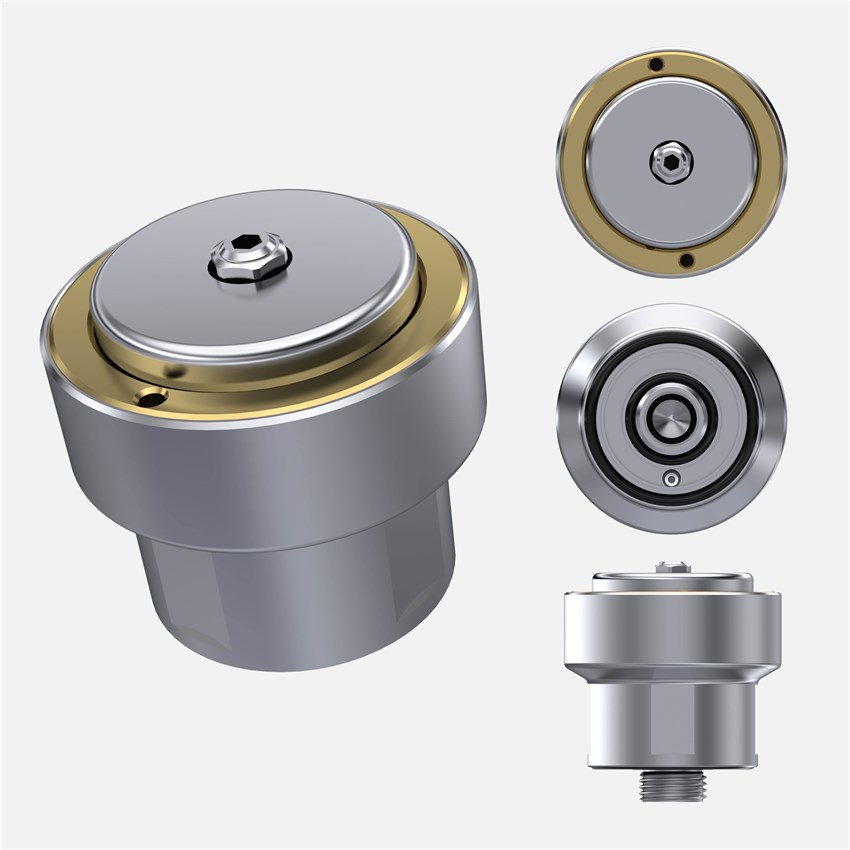
In many applications, it is imperative to control pressure to ensure machinery and devices work optimally and without issue.
Pressure regulators ensure that a constant flow is achieved with little deviation, and offer a reliable and accurate means of controlling pressure. At The West Group, we have over 50 years’ experience in supplying these to the industrial, scientific and medical markets.
Pressure regulators keep downstream pressure constant, regardless of fluctuations in either upstream pressure or the rate of air consumption. This is only true, of course, if the upstream pressure is greater than that of the downstream.
When selecting a suitable pressure regulator, a few key points must be considered to make sure that the regulator is suited to your application. Firstly, we must consider the type of regulator you require.
Regulator Type
There are two types of pressure regulator, the relieving and non-relieving. A relieving pressure regulator will expel excess pressure to the atmosphere, and tend to be used in pneumatic systems to power actuators, air tools, spraying equipment, and nozzles.
In contrast, a non-relieving regulator is used when the escape of a gas or fluid could create a hazard. For example, allowing a vent to expel flammable gases such as propane fuel, oxygen, and inert gases such as nitrogen, would pose a serious danger and would have to be contained internally.
Below is a table showing the variations of both relieving and non-relieving regulators:
No relieving device in the regulator, entirely self-contained
Enables pressure relief on outlet if the pressure rises above the set point, including a zero outlet flow condition
Enables pressure relief on outlet, with bleed to aid accuracy in control of pressure
Thus, for applications where it is imperative to strictly maintain pressure accuracy – such as tension control for a paper roller – the precision regulator would be the superior choice.
Media Compatibility
When selecting a regulator, you must consider the compatibility of the media you will be using, and how this media will affect wetted areas – surfaces that will be exposed to media flowing through the regulator. This is because these wetted areas include internal seals and diaphragms, so if there is no compatibility with the media being used, these can degrade and malfunction easily.
High grade materials such as 316 stainless steel are compatible with many of the gases used in medical and scientific equipment. However, “yellow” metals such as brass are usually suitable for applications using air and inert gases. Should polymers be listed among the materials of the wetted surfaces, extra care is required to check for compatibility with the media being used. One of the more versatile rigid polymers, PPS (Polyphenylene Sulfide), is compatible with some medical gases for example. If there is any doubt, our technical team are available to advise on the best option for your requirements.
Many manufacturers offer a choice of materials for internal seals, and some also offer a choice of diaphragm material. If a lubricant is used by a manufacturer on the seals to either aid assembly, or the movement of the internal mechanism, this may appear on the list of wetted materials – but not always. A check with the manufacturer is therefore advisable to prevent any issues.
Performance
The maximum supply pressure to be used in any application for these regulators should not exceed the maximum working inlet pressure. Additionally, the effect of supply pressure variation on the outlet of a regulator should be checked. This is typically stated as the change in outlet pressure for a 5psi (0.35bar) change in that of the inlet. This parameter is of particular importance where an application has a large range of supply pressure.
The effect of a change in temperature of the regulator body and media on the outlet pressure should also be considered for the operating range of a device. This tends to be described as an mbar/degree Celsius change.
Droop/Accuracy and Hysteresis
Droop has an impact on the overall performance of a regulator. Defined as the deviation from the setpoint as flow increases through a regulator, droop should be taken into consideration to ensure that the system is working optimally. With direct-acting regulators, the outlet pressure at a higher flow is lower than that of the flow used for the set point. A precision regulator will have a lower pressure droop than a general-purpose regulator because it is designed with improved pressure compensation in order to prevent this effect.The usual flow range of a regulator is normally between zero and the flow at which droop causes a significant lowering of outlet pressure below the set point.
The accuracy of a regulator at a given flow and temperature is often defined as repeatability or sensitivity. Repeatability is typically the maximum expected variation in outlet pressure seen when the supply pressure is switched on and off, then on again for a given supply pressure and flow. Consequently, sensitivity is the smallest change in outlet pressure required to cause the regulator diaphragm and control element to move, such as the regulation of outlet pressure.
Mounting Types
For single stage, direct-acting regulators, there are three main types of mounting styles:
- Inline Mounting – these can consist of barb to barb connections or threads to connect pipe/tubing and then mounted on a panel or bracket.
- Manifold Mounting – the regulator is installed on a manifold by torquing a threaded nose of the regulator onto the manifold, with outlet port positioned between seals that interface with a manifold face, straight onto the machine.
- Cartridge Mounting – the regulator is installed in a cavity in the manifold and secured by a clamp plate.
In terms of the most compact types of mounting, both manifold- and cartridge-mounted are the most compact and allow for integration into a manifold to connect with other items of the fluid control circuit. Additionally, they can be installed more quickly than body-mounted versions with less components.
Size and Weight
The size and weight of scientific and medical equipment are important, particularly for equipment where portability is required. Compact, low weight pressure regulators and control valves are key to enabling the manufacture of compact, light weight fluid control devices.
Single Stage vs. Multi Stage
Depending on your application, a single-stage regulator might not quite be fit for use. Where a single-stage pressure regulator reduces pressure in one step, a multi-stage (or two-stage) regulator does this in two steps.
Working out which is the correct regulator for you is dependent on two factors: droop and supply pressure effect. Both regulators respond differently to changing supply pressures and each have different droop characteristics. The single-stage regulator shows little droop with varying flow rates, but is affected by a change in supply pressure significantly. Compared to this, the multi-stage shows considerable droop, but only small supply pressure effects.
A single-stage regulator is recommended where inlet pressure does not vary as much, whereas a two-stage regulator provides a constant and consistent delivery pressure with no need for periodic readjustment.
Conclusion
Medical and scientific devices are becoming more compact and require more complex fluidic systems. With this, the trend is increasing for smaller precision pressure regulators with good repeatability and a wide flow range to reduce system size and weight. This comes with the benefits of compact integration, reducing system assembly time and improve overall system quality.